Do you want to save interesting articles to your personal bookmarks? Please register here:
Already have an account? Please sign in here: Login TR sport outsole mould for Italy
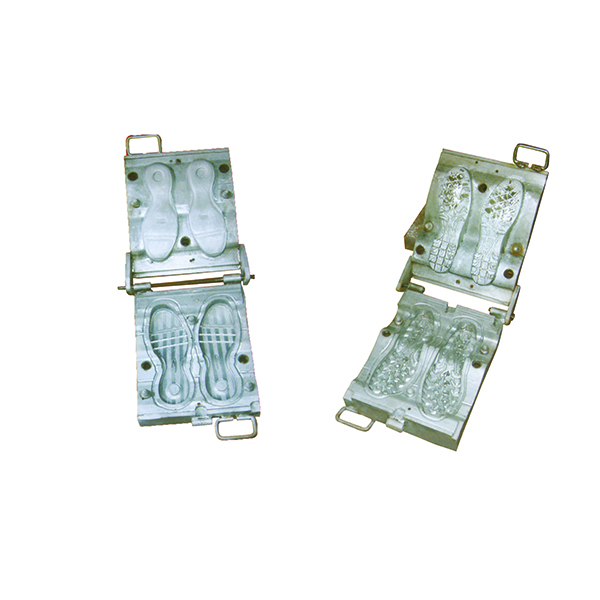
Anyone who wants to be successful in plastic injection moulding today should rely on automation and the right production systems - just like Fuso.
The company Joh. Fuchs & Sohn (Fuso) was founded in 1947 in Waidhofen an der Ybbsitz in Lower Austria. The company entered the field of plastic injection moulding in 1964 with the production of orange-coloured lids for Ovomaltine cans. Today, Fuso employs around 80 people and produces sophisticated plastic parts from a wide variety of materials, including high-temperature plastics, on an area of almost 3,000 square metres.
The components produced range from small parts weighing from 0.03 grams to parts weighing up to two kilograms. In addition to the production of plastic parts using 1- or 2-component injection moulding, the company also offers overmoulding of functional parts, component assembly, bonding and welding as well as finishing using 4-colour pad printing. It also offers laser printing and 3D scanning for reverse engineering. 3D printing with a view to rapid prototyping can also be utilised. Injection moulding tools and automation systems are planned, designed and manufactured by Fuso's in-house toolmaking department.
The demands of Fuso customers in terms of the quality and properties of the parts with regard to tolerances, appearance and the materials used are constantly increasing, however. As the requirements for the produced parts and assemblies increase, so do Fuso's demands on injection moulding technology. The company's machinery is also very new and production relies on automation. All systems are therefore equipped with robots to ensure careful handling of the parts.
Energy efficiency of the machines and systems, connectivity with robots and peripheral devices and assistance systems are also becoming increasingly important.
Injection moulding machines with clamping forces ranging from 450 to 5,200 kilonewtons are used to manufacture the parts, 17 of which are from Wittmann Battenfeld. In addition, Fuso has long been a customer of the Wittmann Group in the automation sector and has over 40 handling devices with a payload of between 5 and 30 kilograms in use, ranging from the robot series 7 to the latest series 9 with R9 control.
The newer machines supplied by Wittmann Battenfeld are exclusively machines from the Smartpower series, according to the company. The machines operate with hydraulic technology and are equipped with fast-reacting servomotors and powerful fixed displacement pumps, says the manufacturer. This technology, combined with the Kers (Kinetic Energy Recovery System) installed as standard to utilise the braking energy within the machine, explains the high energy efficiency of the injection moulding machines. Other characteristics of the Smartpower are the small footprint and the swivelling injection unit, which ensures good accessibility to the screw barrel, making it easy and convenient to change the barrel.
With the exception of one machine, all are designed as insider cells. This means that the Wittmann robot and conveyor belt are integrated into the work cell. This variant offers a number of advantages. These range from space savings compared to systems with conventional automation systems to cost benefits, as all hazardous areas are already protected and fully certified. The robot cycle time can also be minimised thanks to shorter travel distances and the direct placement of the moulded parts on the conveyor belt.
The injection moulding machines delivered in 2023 are already equipped with the new B8X control system and the Hiq Flow assistance system, as Wittmann Battenfeld explains further. The B8X control system also works with control components developed in-house. These enable a higher internal clock frequency and therefore shorter reaction times to sensor signals, resulting in better reproducibility of parts with unchanged ease of operation and familiar visualisation. The Hiq Flow assistance system is an injection control system that can be used to compensate for viscosity fluctuations in the plastic melt. This function enables process automation and compensates for even minimal fluctuations in material quality. According to Wittmann Battenfeld, Fuso was so impressed by the system that it was retrofitted to all machines where it was technically possible and economically viable.
By clicking on „Subscribe to Newsletter“ I agree to the processing and use of my data according to the consent form (please expand for details) and accept the Terms of Use. For more information, please see our Privacy Policy.
Naturally, we always handle your personal data responsibly. Any personal data we receive from you is processed in accordance with applicable data protection legislation. For detailed information please see our privacy policy.
I hereby consent to Vogel Communications Group GmbH & Co. KG, Max-Planck-Str. 7/9, 97082 Würzburg, Germany, including any affiliated companies according to §§ 15 et seq. AktG (hereafter: Vogel Communications Group) using my e-mail address to send editorial newsletters. A list of all affiliated companies can be found here
Newsletter content may include all products and services of any companies mentioned above, including for example specialist journals and books, events and fairs as well as event-related products and services, print and digital media offers and services such as additional (editorial) newsletters, raffles, lead campaigns, market research both online and offline, specialist webportals and e-learning offers. In case my personal telephone number has also been collected, it may be used for offers of aforementioned products, for services of the companies mentioned above, and market research purposes.
In case I access protected data on Internet portals of Vogel Communications Group including any affiliated companies according to §§ 15 et seq. AktG, I need to provide further data in order to register for the access to such content. In return for this free access to editorial content, my data may be used in accordance with this consent for the purposes stated here.
I understand that I can revoke my consent at will. My revocation does not change the lawfulness of data processing that was conducted based on my consent leading up to my revocation. One option to declare my revocation is to use the contact form found at https://contact.vogel.de. In case I no longer wish to receive certain newsletters, I have subscribed to, I can also click on the unsubscribe link included at the end of a newsletter. Further information regarding my right of revocation and the implementation of it as well as the consequences of my revocation can be found in the data protection declaration, section editorial newsletter.
5,700 customers visit Arburg Anniversary Days 2023 in Lossburg
How hot runner design and technology can positively impact sustainability goals
Imprint Cookie-Manager About Media Privacy General Terms and Conditions Help
Copyright © 2024 Vogel Communications Group

High Heel Pvc Crystal Mould This portal is a brand of Vogel Communications Group. You will find our complete range of products and services on www.vogel.com